厂中厂模式的拓路者效应
- 2025-07-23 17:30:00


近日,宁德时代位于重庆的首条动力电池生产线在赛力斯问界超级工厂投产。两条CTP2.0高端电池包生产线的启用,不仅标志着宁德时代在重庆布局的初步落成,更是车企与供应链“厂中厂”合作模式的探索。在“反内卷”呼声日益高涨的当下,汽车行业正朝着高质量发展迈进。宁德时代与赛力斯携手打造的“厂中厂”合作模式,有望为汽车产业构建高效协作的生产关系提供探路和示范效应。
“强强联手”锚定双赢

“今天投产的这条生产线,是宁德时代最先进的智能化、数字化产线。”宁德时代董事长兼首席执行官曾毓群为此次投产定性,这不仅标志着宁德时代在重庆本地化生产的开端,更是与问界合作的新起点。问界自创立以来,全系车型均搭载宁德时代电池,累计市场保有量已突破70万辆。
今年上半年,得益于M8、M9等热门车型的上市,赛力斯销量迅速提升,盈利能力显著增强。1~6月,公司累计批发销量达19.86万辆,其中新能源汽车销量为17.21万辆,预计上半年实现归母净利润27.00亿元至32.00亿元,同比增长66.20%至96.98%。在市场火热、盈利可观的背景下,加快投产成为赛力斯的必然选择。电池作为核心零部件,其配套供应能否跟上,将是决定赛力斯能否继续保持优势的关键。
毫无疑问,宁德时代此次采用“厂中厂”模式投产,将电池生产线直接建于赛力斯超级工厂内,实现了动力电池从下线到装车的高效闭环管理,进一步助力问界提升生产及交付速度,缩短用户提车周期。据介绍,宁德时代采用最先进的智能化、数字化生产线,专供问界全系车型,涵盖M9、M8等旗舰产品。投产后,电池生产实现“即产即装”,省去包装、运输、仓储等中间环节,供应链响应速度提升至20分钟级(传统模式需数日)。
更为利好的是,赛力斯超级工厂作为全球最先进的标杆工厂之一,具备高效、智能、尖端、绿色四大特质。宁德时代也将发挥零碳科技公司的优势,协助赛力斯打造一条完整的“绿色汽车价值链”,强化“零碳智造”的全球品牌形象。赛力斯集团董事长张兴海认为,宁德时代的电池生产线落地重庆,具有里程碑意义。
此前,双方已将合作拓展至零碳领域,联合打造并成功并网赛力斯超级工厂一期50MWh分布式光伏项目,为工厂提供核心绿色能源。未来,宁德时代与赛力斯将长期携手,深化在新产品研发、新技术与新材料应用等领域的战略协同,推进全产业链绿色低碳转型,引领中国新能源汽车产业链迈向更高质量的发展阶段。

赛力斯超级工厂新成员

在一个大型工厂内部,由于生产流程的复杂性和产品种类的多样性,通常会划分出不同的生产区域或车间。这些区域或车间专注于特定的生产环节或产品类型,拥有相对独立的生产线和作业团队。尽管它们隶属于同一个大厂的管理体系,但具备较高的自主性和独立性。这种模式被称为“厂中厂”,它不仅有助于提高生产效率、降低成本,还能通过专业化的分工提升产品质量。
这种生产组织模式使企业能够根据市场需求灵活调整生产布局。当某个产品或生产环节需要特殊技术或管理时,企业可以在厂内设立专门的工厂或车间来满足这些需求。同时,“厂中厂”模式也有助于企业实现资源的集中管理和高效利用,确保各生产环节之间的顺畅协作。此外,该模式还能帮助企业构建完善的生产体系,提升整体竞争力。
对于赛力斯而言,“厂中厂”模式并不陌生。几年前,在与华为基因融合后,赛力斯在生产制造中探索出了这一新方向。2024年,央视总台探访了赛力斯的超级工厂,发现工厂内部并存着多个供应商。经过仪表台的产线,推开一扇门,便进入了生产汽车座椅的工厂。由于产线相邻,沟通及时,座椅供应商表示:“到客户那边响应时间可能只需20分钟左右。”再穿过一道门,便是车身压铸件工厂。“我们这个厂已经成为整车制造的一个单元,真正实现了‘你中有我、我中有你’的大融合。”汽车车身压铸件供应商表示。
赛力斯超级工厂通过“厂中厂”模式,达到了极高的生产效率。例如,冲压环节可实现每分钟生产16个零件,工厂内部实现100%自动化转运、焊接自动化率100%、喷涂自动化率100%等。在质量控制方面,赛力斯应用了IOT物联网平台,从板材进线到整车下线的全过程中,实现质量数据的100%自动采集和分析,确保最终产品不受影响。
“厂中厂”、“门对门”的模式使赛力斯与供应商紧密合作,问题能够迅速协商处理。从发现问题到上下游同时到位,不惜停机检查,迅速排查,迅速补漏,再次复工。这种模式极大提升了整个产业链的协同效率,成为赛力斯快速提升产能的关键因素。

产业链合作新范本

总地来说,“厂中厂”是企业为提升生产效率、降低成本、增强市场竞争力而采取的一种生产组织策略。在这种模式下,各个“厂中厂”之间既存在合作也有竞争,共同构成了大型企业的整体运营体系。这种模式有助于企业适应不断变化的市场环境,并实现可持续发展。
传统的“厂中厂”模式,多采用租赁场地的方式,主要目的是获取建设、生产许可,如安全生产许可证、环评批复、排污许可证等。一位业内人士向记者透露,这一模式并非新生事物,只是以往更多是出于“无奈之举”,例如企业缺乏生产资质、场地或污染治理能力,不得不租赁现有厂房,这在某种程度上也盘活了闲置资源。
然而,这种模式带来的隐患也不少。以往“厂中厂”模式的违规事故频发,如管理责任不清晰、经营状况不透明等问题,使这一模式一度被贴上“小作坊”的标签。为加强精细化管理,江苏等多地的应急管理部门已建立了一套系统的《厂中厂安全生产管理实施方案》,按照“排查整改—规范提升—标准化推进”的工作路径,厘清各方安全生产责任。
目前,以赛力斯为先驱构建的“厂中厂”模式新范本,本质上是强势零部件厂商与主机厂资本合作后的深度延伸。车夫咨询合伙人曹广平认为,这种模式不仅具备传统“厂中厂”的优势,如利用现有厂房投入新产线,减少新工厂建设的时间、资金、人力、物流管理等成本,还具有新式合作的优势,能够在技术资源配置、生产制造工艺、人力装备环节等方面实现交叉调节和共用共享,尤其是在高自动化、高质量要求的环节。重庆市经信委将“厂中厂”模式评价为“重庆打造智能网联新能源汽车之都的标志性成果”,为新能源汽车产业链的垂直整合提供了新思路,有望引发行业内更多的效仿和创新。
随着新能源汽车产业竞争进入新阶段,从单一产品竞争转向生态协同能力的对决,“厂中厂”作为供应商与主机厂共同探索的供应链协同新机制,在这种全新的模式下,核心零部件供应商直接集成到整车制造工厂内部,实现高效协同和快速响应,助力整车厂提升产能并缩短交付周期。
然而,仍需注意的是,“厂中厂”模式的合作具有独特性,需以零部件企业与主机厂的强力资本合作为基础,以减少经营风险。同时,可能面临供应单一、创新排异以及质量事故扩大化等风险。曹广平直言,在这种模式创新中,更需要加强各方面的支撑,包括双重供应保护机制、柔性保护框架、质量事故交叉风控等,并且双方各自仍需保留一定的事故熔断、后门输入和紧急输出的渠道和预案,即在实现“厂中厂”的同时,还要注意合作中的“能松能紧”。
文: 张雅慧 编辑:郭晨 版式:刘晓烨


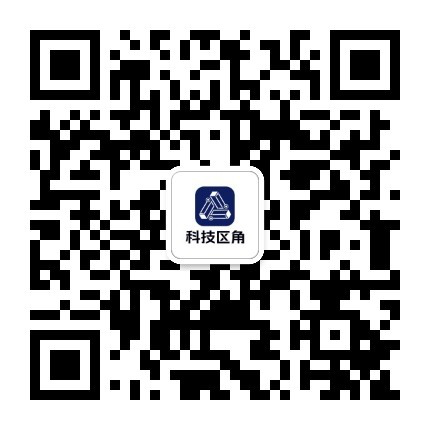
- 点赞 (0)
-
分享
微信扫一扫
-
加入群聊
扫码加入群聊