玻璃基板化学镀铜方法研究
- 2025-07-21 16:04:03
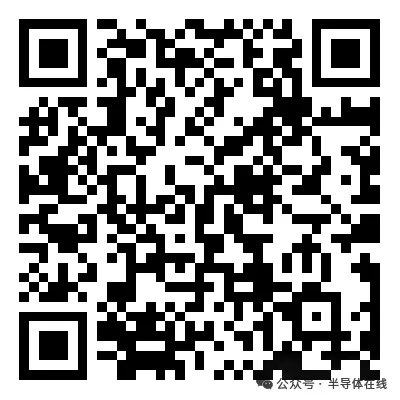
摘要
镀铜玻璃在电子产品、通信设备等领域有着广泛的应用,玻璃与铜层的附着力至关重要,但 玻璃表面本身具有化学惰性和光滑的表面特性不利于铜层附着。本文研究了一种提高玻璃镀 铜附着力的方法,通过在玻璃表面涂敷一层超薄的二氧化钛薄膜,而后通过化学沉积法在玻 璃表面制备不同厚度的氧化锌金属氧化物,经过高温烧结后进行化学沉铜。测试结果显示, 镀铜加厚至20 µm时附着力大于6 N/cm。处理介厚400 µm/孔径50 µm的通孔,孔壁沉铜层 覆盖完全,厚度均匀,为后续玻璃通孔(Through Glass Via,TGV)电镀填孔打下了良好基础。
在半导体和微电子封装技术中,玻璃具有优异的机械性能、较高的热稳定性及较高的平整度等优点,而在玻璃 上镀铜又具有优异的导电性,因此镀铜玻璃在电子产品、通信设备等领域有着广泛的应用。然而,在这些应用中,玻璃 与铜层的附着力至关重要,良好的附着力可以确保电极的可靠性和机械稳定性,从而避免因热应力或电流负载导致界面 剥离或失效。但玻璃表面本身具有化学惰性和光滑的表面特性不利于铜层附着。因此,本文实验研究了在玻璃表面通 过化学沉积法覆盖一层金属氧化物薄膜,作为粘结层,提高玻璃与铜层之间的附着力。
1 实验部分
1.1 实验步骤
实验采用介厚400 μm/孔径50 μm的TGV玻璃基板。如图1所示,首先对玻璃进行清洁,接着将清洁后的玻璃片用钛 酸酯偶联剂进行表面改性并将溶剂进行干燥;浸入可溶性锌盐与碱溶液混合形成的络合物溶液,通过化学沉积法制备一 层氧化锌薄膜,将其进行高温烧结形成带有粘结层的玻璃基板;随后进行化学镀铜,形成种子层;进行填孔电镀,电镀 铜厚约20 μm进行退火,镀铜后进行退火可降低基材应力,后进行260 ℃回流焊测试。
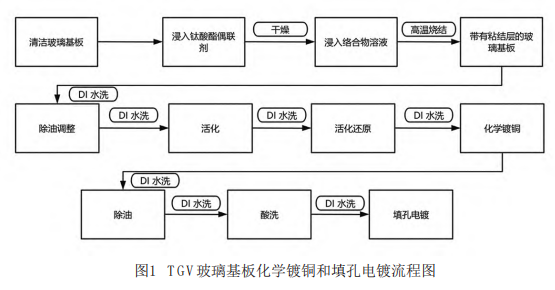
以上简要概括为四个步骤:
(1)玻璃基板清洁;
(2)依次浸入钛酸酯偶联剂和络合物溶液,烧结后得带有粘结层的玻璃基板;
(3)进行化学镀铜和电镀铜,化学铜厚为0.3~0.5 μm,电镀铜厚约20 μm,退火;
1.2 金属氧化物形貌表征及性能测试
1.2.1 金属氧化物表面形貌表征测试
使用扫描电子显微镜(SEM)对金属氧化物表面形态进行观测,并且观察玻璃基板与金属氧化物、金属氧化物与铜 层之间是否有裂缝、空洞。通过能量分散谱仪(EDS)分析玻璃基板、表面金属氧化物及铜层所含元素和相应含量。
1.2.2 玻璃基板与铜层之间附着力测试
使用剥离强度测试仪进行附着力测试,将约20 μm的铜层与玻璃基板呈90°进行剥离试验,观测铜层与玻璃基板之 间附着力变化。
1.2.3 背光测试和切片测试
使用奥林巴斯BX53M显微镜2.5X背光镜头观察TGV孔型是否完整,后对TGV进行切片观察,使用20X镜头进一步观 察孔内铜层均匀性及是否存在孔破。
2 结果与讨论
2.1 玻璃表面金属氧化物粘结层形貌及粗糙度
当玻璃基板浸入锌络合物溶液进行化学沉积,沉积15次后进行烧结(如图2A),形成均匀的白色涂层,其粗糙度Ra 为224 nm。将玻璃基板进行化学镀铜后(如图2B),化学镀铜覆盖完全且均匀,为后续电镀提供一层良好的种子层。 粘结层高温烧结后,使用激光显微镜对其表面进行粗糙度测试,玻璃基板表面出现许多“针状”晶粒,(如图 3A),后使用SEM对表面观测,进一步确认玻璃基板表面生成“针状”晶粒,此“针状”晶粒随着金属氧化物沉积次 数的增加而增加,金属氧化物沉积次数越多,其表面形成的“针状”晶粒越密集,粗糙度随之增大,玻璃基板与铜之间 的附着力越强(如图3B)。

2.3 TGV孔壁金属氧化物粘结层的形貌及成分分析
图4为TGV孔壁金属氧化物粘结层SEM图,其中图4A是通孔孔型全貌图,结果显示孔内铜层覆盖完全且均匀,后将 孔壁表面用离子研磨抛平,使用SEM观测孔壁与金属氧化物粘结层、金属氧化物粘结层与铜层之间是否有裂缝、空洞如 图4B、图4C。结果表明,各膜层之间无裂缝、无空洞,粘接良好,进一步说明玻璃基板与铜之间附着力强,且在孔壁 和表面能形成均匀厚度的铜层。
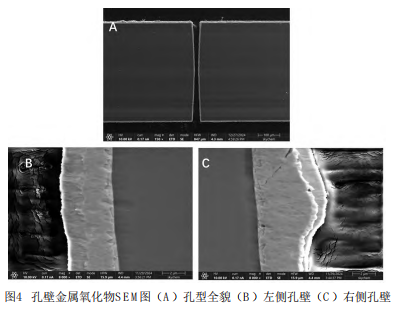
通过FIB观测孔内薄膜情况,并使用EDS进行孔壁附近元素分析(如图5)。其中Spectrum1对应玻璃基板, Spectrum2对应金属氧化物粘结层,Spectrum3为对应化学镀铜所得铜层,Spectrum4为对应电镀所得铜层,图5中Spectrum1、Spectrum2、Spectrum3和Spectrum4对应的元素结果(见表1、表2、表3、表4),对应的成分分析图(如图 6)。结果表明,Spectrum2对应位置含有0.95%钛元素和29.77%锌元素,说明成功制备金属氧化物粘结层。
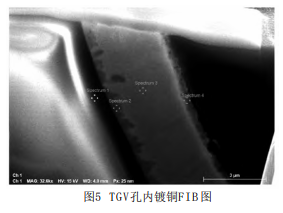
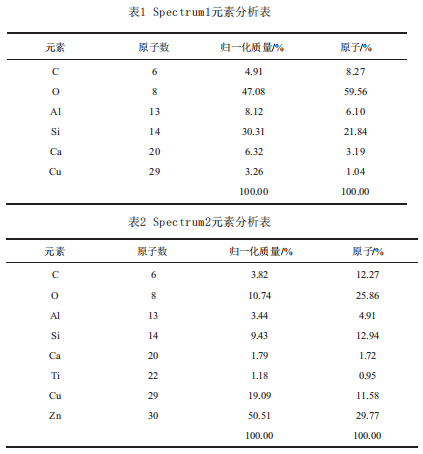
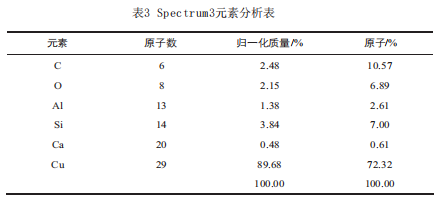
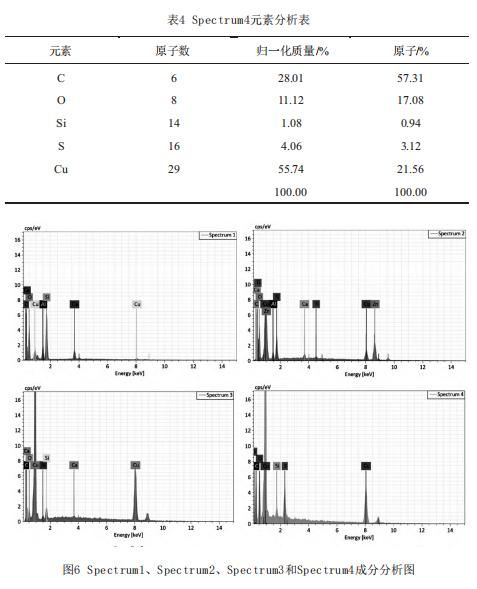
2.4 不同沉积次数的金属氧化物对附着力的影响
图7为附着力与金属氧化物沉积次数的变化关系图,当沉积5次金属氧化物时,电镀膜厚20 μm后平均附着力为6.85 N/cm, 粗糙度Ra为0.113 μm。当沉积10次金属氧化物时,电镀膜厚20 μm后平均附着力为7.68 N/cm,粗糙度Ra为0.19 μm;当沉积15次 金属氧化物时,电镀膜厚20 μm后平均附着力为8.17 N/cm,粗糙度Ra为0.211 μm。当沉积30次金属氧化物时,电镀膜厚20 μm后 平均附着力为8.91 N/cm,粗糙度Ra为0.352 μm。由此结果表明粗糙度与附着力随着沉积金属氧化物的次数增加而逐渐增 大,由于沉积次数增加,附着在玻璃基板的金属氧化物形成的“针状”晶粒越密集,粗糙度越大,附着力也随之增大。 后经过260 ℃回流焊测试,未鼓泡、未分层,且附着力无明显变化。
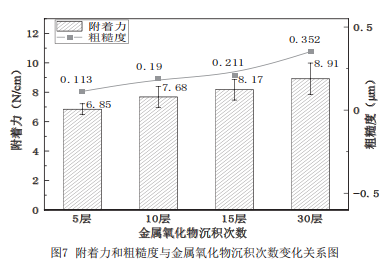
2.5 金属氧化物对不同孔径TGV堵孔性测试
图8为不同孔径TGV闪镀后效果图,其中A、B为80 μm和50 μm孔径TGV背光图,结果显示其孔形完整,无明显堵 孔情况,将其进行切片观察,其中C、D分别对应80 μm和50 μm孔径TGV闪镀后切片图,结果显示其孔壁覆盖完全,镀 铜均匀,无堵孔情况。

3 结论
玻璃表面制备金属氧化物提高其与铜层之间附着力,且进行回流焊测试后无鼓泡、分层,附着力几乎不变,保持 6 N/cm以上,可有效解决由于玻璃表面光滑导致与铜层附着力差的问题。通过背光测试和切片测试未发现堵孔情况, 且孔内铜层覆盖完全且均匀,为后续TGV电镀填孔打下了良好基础。
来源:HDI板与载板
作者:刘明迪 李晓红 邵永存 章晓冬 刘江波

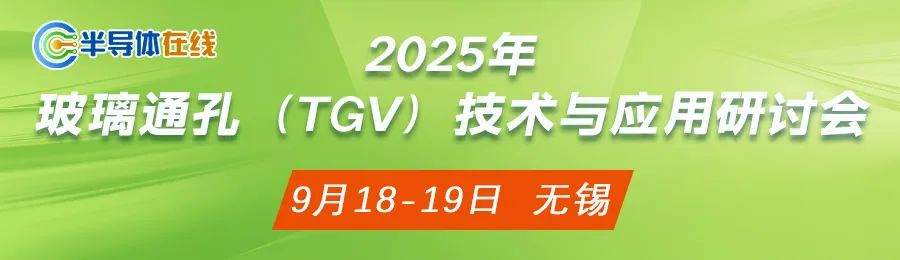
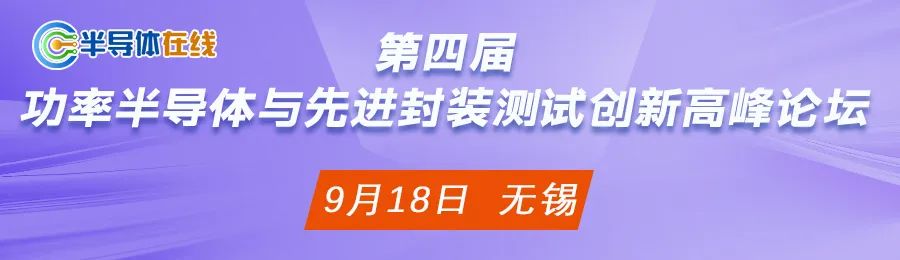
点击左下方阅读原文,立即报名玻璃通孔(TGV)技术与应用研讨会!

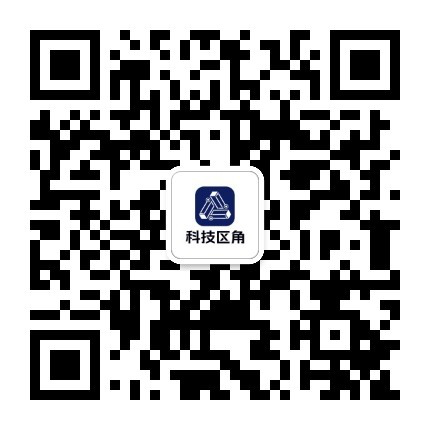
- 点赞 0
-
分享
微信扫一扫
-
加入群聊
扫码加入群聊